
Granted, you need to have the patience to read the manual, as it might take several minutes before you find a solution to the problem at hand. If you purchased the compressor fairly recently, an improper adjustment could render the warranty null and void. Failure to follow this step could cost you down the line. However, you should never try to fix anything on your air compressor without first reading through the user manual. A none-too-uncommon mistake in cases like these is for the operator to tinker with things manually in the hope of fixing the problem.
Air compressor pump manual#
While this might sound like a no-brainer, many owners of air compressors forget entirely about the manual and instead resort to distress calls, even for some of the most easily remedied issues.įor instance, there might be an issue with one of the connections or inlets that won’t initially make sense. Some of the most common problems with an air compressor are easy to solve with the help of the user manual. Basically, a compressor needs to have its oil changed, its filters cleaned and its after cooler inspected every three months, and have its filters replaced and connections tightened at least once every year. As such, an air compressor consists of various parts, each of which must be maintained to ensure their proper function.
Air compressor pump series#
Air Compressor Maintenance TipsĪn air compressor employs a series of processes that turn incoming ambient air into a power source for tools and machinery.
Air compressor pump full#
Use the following air compressor maintenance guide to ensure your machines function at full capacity. With timely, proper maintenance, you can avoid the setbacks and financial pitfalls that often accompany air compressor failure. Of course, the same could be said for any company that works with air compressors, regardless of whether the machines are used for light or heavy-duty productions. These projects get funded according to strict timetables that can only be fulfilled with functioning tools and machinery.Īs such, no construction crew can properly manage itself without a rotary screw air compressor maintenance checklist. Just consider all the money that is on the line with major construction projects, where city governments and investment firms commission new buildings, monuments, stadiums and recreational facilities. Without this sort of schedule, a company could easily lose track of which machines and parts have not yet undergone maintenance.įor obvious reasons, the stakes are especially high when it comes to rotary screw air compressor maintenance. This way, you can easily keep track of which maintenance steps you need to perform during a given day, week, month, season or year. Given the cumulative nature of performance issues, all companies need to implement an air compressor maintenance schedule. Neglecting such steps, however, could result in costly repair bills down the line. After all, certain preventive steps are easy to learn and only take a few minutes to complete. When you think about the way minor problems can easily grow into major problems when not remedied in time, air compressor preventive maintenance can save both money and time. If one of these compressors breaks down on the job, a construction crew could fall drastically behind schedule. The powering of pneumatic jackhammers, for instance, relies on rotary screw compressors, which are common at construction sites. Rotary screw air compressor maintenance is especially important because of the high-powered tools that rely on such machines. Consequently, calls to service specialists are a common occurrence. However, many of these same companies lack the on-site talent to service air compressors as needed. Companies that serve all sorts of industries across the private sector rely on compressed air.

The failure of an industrial compressor can result in costly downtime.ĭue to the high stakes at play, commercial air compressor maintenance has become an industry unto itself.
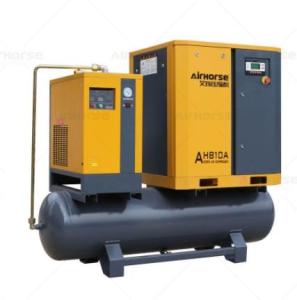
With so many machines, tools and functions relying on compressed air, it is crucial to ensure every compressor within an industrial setting is capable of performing as needed when needed.

Failure to do so could result in premature failure and costly repairs.Īt factories and pressing plants, industrial air compressor maintenance is one of the crucial areas of system management. Whether you operate one compressor or several, you should routinely inspect key components of the machine and service them, if necessary. Air compressor maintenance involves a set of practices that need to be performed to varying degrees on compressors of all makes and models.
